We love all that flies.
-Those Fantastic Flying Machines-
NEWS AND ANNOUNCEMENTS
Search This Blog
Some links may have expired
Ghetto List
Thursday, May 31, 2012
Wednesday, May 30, 2012
Air Force's mini space shuttle prepares for landing
Air Force's mini space shuttle prepares for landing
BY JUSTIN RAY
SPACEFLIGHT NOW
Posted: May 30, 2012


The base, located about 150 miles northwest of Los Angeles, announced Wednesday that preparations are underway to receive the second reusable spaceplane in the "the early- to mid-June timeframe."
Launched atop an Atlas 5 rocket from Cape Canaveral on March 5, 2011, the winged craft has been operating in low-Earth-orbit carrying out a mission of unknown purpose. The military considers the payload classified.
BY JUSTIN RAY
SPACEFLIGHT NOW
Posted: May 30, 2012


After 15 months circling the planet on its clandestine military mission, the Pentagon's miniature space shuttle will be coming back to Earth for a pinpoint touchdown at Vandenberg Air Force Base in the next couple of weeks.
![]() File image of first X-37B spaceplane on the runway after landing at Vandenberg Air Force Base in 2010. Credit: Air Force |
The exact landing date and time "will depend on technical and weather considerations," the base said in a statement to reporters.
The Orbital Test Vehicle will use Vandenberg's three-mile-long concrete runway once envisioned to support manned space shuttle landings from polar-orbiting military flights.
"The men and women of Team Vandenberg are ready to execute safe landing operations anytime and at a moment's notice," said Col. Nina Armagno, 30th Space Wing commander.
Operating on a sophisticated autopilot and GPS navigation, the OTV will fire its propulsion system to brake from orbit and plunge through the atmosphere over the Pacific Ocean towards the Air Force installation for a tire-smoking touchdown.
"Space professionals from the 30th Space Wing will monitor the de-orbit and landing of the Air Force's X-37B Orbital Test Vehicle mission, called OTV 2," Vandenberg's statement said.
The base said its crews have conducted extensive, periodic training in preparation for landing.
![]() Photo of the first X-37B spaceplane on the runway after landing at Vandenberg Air Force Base in 2010. Credit: Boeing |
Its pickup truck-size payload bay could be filled with experimental equipment being exposed to the harsh environment of space for proof testing or the cargo hold could contain operational instruments for reconnaissance.
"Although I can't talk about mission specifics, suffice it to say this mission has been a spectacular success," General William L. Shelton, commander of Air Force Space Command, said in a recent speech.
Built by Boeing's Phantom Works division, the spaceplane is 29 feet long with a wing span of 14 feet. It can weigh up to 11,000 pounds fueled for launch. The in-space design life is 270 days, but good performance on this mission enabled ground controllers to keep it aloft significantly longer.
Hobbyist satellite trackers have kept close tabs on the vehicle since its launch, monitoring it in an initial 206-mile (331 km) orbit inclined 42.8 degrees to the equator. Last summer, the orbit was raised slightly to 209 miles (337 km).
"It maintained this altitude against the effects of drag through frequent small orbit maneuvers," said Ted Molczan, a respected hobbyist tracker.
Earlier this month, however, the craft began lowering its altitude, briefly slipping out of the observers' sight until being discovered in the new orbit of 182 miles (293 km) tilted 41.9 degrees relative to the equator.
The new orbit causes its ground track to repeat, almost precisely, every three days; the previous altitude repeated every two days. Molczan said satellites with ground tracks repeating at intervals of two, three or four days have long been favored for U.S. imagery intelligence satellites, potentially offering a clue to the craft's mission.
This is the second of the Orbital Test Vehicles to fly in the X-37B program, following the maiden mission in 2010 that spent 224 days in space, frequently maneuvering in what was considered to be a shakedown cruise to demonstrate the spaceplane's capabilities.
The original vehicle has been refurbished for shipment to Cape Canaveral and a return to space. Another United Launch Alliance Atlas 5 rocket will haul the craft to orbit in a liftoff targeted for October.
Tuesday, May 29, 2012
Sunday, May 27, 2012
Friday, May 25, 2012
Thursday, May 24, 2012
Wednesday, May 23, 2012
Tuesday, May 22, 2012
Monday, May 21, 2012
Saturday, May 19, 2012
Friday, May 18, 2012
American Air Power
![]() |
F-18 Hornet |
![]() |
F-86 Sabre |
![]() |
Grumman E-2 Hawkeye |
![]() |
F-16 Falcon |
![]() |
F-14 Tomcat |
![]() |
F-4 Phantom |
![]() |
Blue Angel F-18 Hornet |
Thursday, May 17, 2012
Wednesday, May 16, 2012
NASA intends to use Delta 4 upper stage on moon flights
NASA intends to use Delta 4 upper stage on moon flights
BY STEPHEN CLARK
SPACEFLIGHT NOW
Posted: May 15, 2012


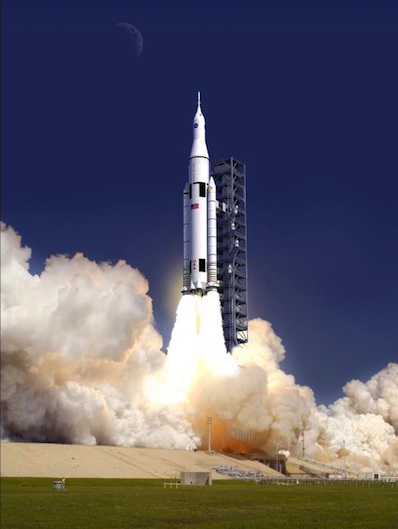
Artist's concept of the Space Launch System. Credit: NASA
The space agency issued a sole-source award to Boeing on April 27 for a feasibility study on the compatibility of the Delta Cryogenic Second Stage, or DCSS, with the Space Launch System, a heavy-lift rocket designed to dispatch astronaut crews on expeditions to the moon, asteroids, Mars, and other deep space destinations.
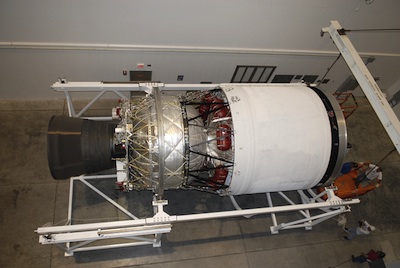
File photo of a Delta 4 second stage. Credit: NASA
The interim cryogenic propulsion stage for the first Space Launch System flight must be delivered to the Kennedy Space Center by the end of 2016 for an unmanned test launch of the mega-rocket and 26.5-ton Orion spacecraft in 2017. The flight will send the Orion capsule on a free return trajectory around the moon and back to Earth for a splashdown landing in the ocean.
BY STEPHEN CLARK
SPACEFLIGHT NOW
Posted: May 15, 2012


NASA says Boeing is best equipped to provide two cryogenic upper stages derived from the Delta 4 rocket to power the agency's Orion capsule on a test flight around the moon in 2017 and send astronauts on a voyage to lunar orbit in 2021, according to documents posted on a federal government procurement website.
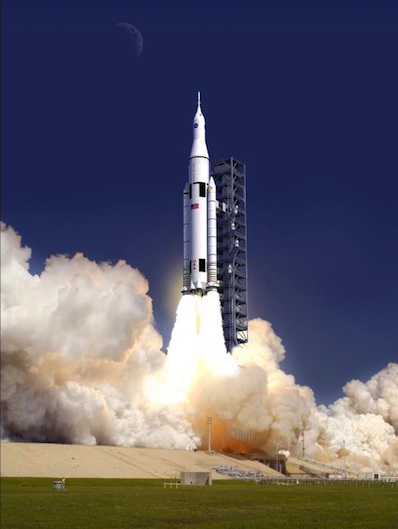
Artist's concept of the Space Launch System. Credit: NASA
The space agency issued a sole-source award to Boeing on April 27 for a feasibility study on the compatibility of the Delta Cryogenic Second Stage, or DCSS, with the Space Launch System, a heavy-lift rocket designed to dispatch astronaut crews on expeditions to the moon, asteroids, Mars, and other deep space destinations.
The $2.4 million contract also covers an evaluation of the upper stage against NASA's human-rating requirements. Boeing will also determine what modifications are needed for the Delta 4 second stage to fly with the Space Launch System.
The Delta 4's hydrogen-fueled upper stage includes an RL10B-2 engine built by Pratt & Whitney Rocketdyne, or PWR. The engine generates 24,750 pounds of thrust and has flawlessly flown on all 19 Delta 4 missions to date.
Space agency officials declined comment on the upper stage acquisition until they formally select a procurement strategy.
But NASA released a justification document for the sole-source study award to Boeing, outlining internal market research and a public request for information solicitation which indicated the Delta 4 second stage is the only propulsion system available to meet NASA requirements.
"The DCSS appears to be the only solution mature enough to meet the requirements of the government within the timeframe needed to support the government's need date for initial delivery," NASA officials wrote in the justification document.
In a presolicitation notice posted May 3 on the Federal Business Opportunities website, NASA wrote it "determined that the DCSS is the only means available to support the immediate in-space propulsion needs of the SLS."
Boeing maintains the design data and manufacturing skills to modify the Delta 4 upper stage for the Space Launch System, according to NASA. United Launch Alliance, a partnership between Boeing and Lockheed Martin, currently builds the Delta 4 and Atlas 5 rocket fleets.
NASA is accepting proposals and quotes from other rocket contractors through May 18, and the agency will use the data to determine whether to conduct a competitive procurement for the SLS upper stage.
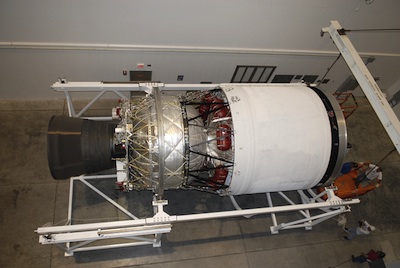
File photo of a Delta 4 second stage. Credit: NASA
The interim cryogenic propulsion stage for the first Space Launch System flight must be delivered to the Kennedy Space Center by the end of 2016 for an unmanned test launch of the mega-rocket and 26.5-ton Orion spacecraft in 2017. The flight will send the Orion capsule on a free return trajectory around the moon and back to Earth for a splashdown landing in the ocean.
"We're in a very constrained budget environment, so it's going to have to come in on mark and show up in time for that first flight," said Todd May, NASA's Space Launch System program manager.
NASA's proposed budget for the SLS program calls for nearly $1.4 billion per year through fiscal year 2017.
The second mission of the SLS and Orion vehicle, tentatively scheduled for 2021, will launch an astronaut crew into orbit around the moon for three or four days, according to current plans.
The RL10B-2 engine on the first two SLS flights would inject the Orion spacecraft into low Earth orbit, then accelerate the capsule on a course toward the moon. NASA says the upper stage engine must be capable of igniting three times on each SLS mission.
The J-2X engine will ultimately fly on the upper stage on future missions of NASA's Space Launch System.
But NASA has put development of the J-2X engine on the back burner while engineers race to ready the Space Launch System for its initial test launch before the end of 2017.
The launches in 2017 and 2021 will use a version of the Space Launch System designed to lift at least 70 metric tons, or 154,000 pounds, into low Earth orbit. The earliest flights will feature a rocket standing up to 320 feet tall powered by a 27.5-foot diameter core stage and twin solid rocket motors derived from motors flown on the space shuttle.
The colossal rocket's cryogenic core stage will be propelled by four space shuttle main engines, known as RS-25D/E engines, provided by PWR. The engines are left over from the space shuttle program.
Tuesday, May 15, 2012
Monday, May 14, 2012
The Jets of the Future
How NASA and aircraft engineers intend to shape the future of air travel

Box Wing Jet Nick Kaloterakis
NASA asked the world’s top aircraft engineers to solve the hardest problem in commercial aviation: how to fly cleaner, quieter and using less fuel. The prototypes they imagined may set a new standard for the next two decades of flight.
BOX WING JET, LOCKHEED MARTIN
Target Date: 2025
Passenger jets consume a lot of fuel. A Boeing 747 burns five gallons of it every nautical mile, and as the price of that fuel rises, so do fares. Lockheed Martin engineers developed their Box Wing concept to find new ways to reduce fuel burn without abandoning the basic shape of current aircraft. Adapting the lightweight materials found in the F-22 and F-35 fighter jets, they designed a looped-wing configuration that would increase the lift-to-drag ratio by 16 percent, making it possible to fly farther using less fuel while still fitting into airport gates.
Passenger jets consume a lot of fuel. A Boeing 747 burns five gallons of it every nautical mile, and as the price of that fuel rises, so do fares. Lockheed Martin engineers developed their Box Wing concept to find new ways to reduce fuel burn without abandoning the basic shape of current aircraft. Adapting the lightweight materials found in the F-22 and F-35 fighter jets, they designed a looped-wing configuration that would increase the lift-to-drag ratio by 16 percent, making it possible to fly farther using less fuel while still fitting into airport gates.
They also ditched conventional turbofan engines in favor of two ultrahigh-bypass turbofan engines. Like all turbofans, they generate thrust by pulling air through a fan on the front of the engine and by burning a fuel-air mixture in the engine’s core. With fans 40 percent wider than those used now, the Box Wing’s engines bypass the core at several times the rate of current engines. At subsonic speeds, this arrangement improves efficiency by 22 percent. Add to that the fuel-saving boost of the box-wing configuration, and the plane is 50 percent more efficient than the average airliner. The additional wing lift also lets pilots make steeper descents over populated areas while running the engines at lower power. Those changes could reduce noise by 35 decibels and shorten approaches by up to 50 percent.—Andrew Rosenblum

Supersonic Green Machine: Nick Kaloterakis
SUPERSONIC GREEN MACHINE, LOCKHEED MARTIN
Target Date: 2030
The first era of commercial supersonic transportation ended on November 26, 2003, with the final flight of the Concorde, a noisy, inefficient and highly polluting aircraft. But the dream of a sub-three-hour cross-country flight lingered, and in 2010, designers at Lockheed Martin presented the Mach 1.6 Supersonic Green Machine. The plane’s variable-cycle engines would improve efficiency by switching to conventional turbofan mode during takeoff and landing. Combustors built into the engine would reduce nitrogen oxide pollution by 75 percent. And the plane’s inverted-V tail and underwing engine placement would nearly eliminate the sonic booms that led to a ban on overland Concorde flights.
The first era of commercial supersonic transportation ended on November 26, 2003, with the final flight of the Concorde, a noisy, inefficient and highly polluting aircraft. But the dream of a sub-three-hour cross-country flight lingered, and in 2010, designers at Lockheed Martin presented the Mach 1.6 Supersonic Green Machine. The plane’s variable-cycle engines would improve efficiency by switching to conventional turbofan mode during takeoff and landing. Combustors built into the engine would reduce nitrogen oxide pollution by 75 percent. And the plane’s inverted-V tail and underwing engine placement would nearly eliminate the sonic booms that led to a ban on overland Concorde flights.
The configuration mitigates the waves of air pressure (caused by the collision with air of a plane traveling faster than Mach 1) that combine into the enormous shock waves that produce sonic booms. “The whole idea of low-boom design is to control the strength, position and interaction of shock waves,” says Peter Coen, the principal investigator for supersonic projects at NASA. Instead of generating a continuous loop of loud booms, the plane would issue a dull roar that, from the ground, would be about as loud as a vacuum cleaner.—Andrew Rosenblum

Sugar Volt: Nick Kaloterakis
SUGAR VOLT, BOEING
Target Date: 2035
The best way to conserve jet fuel is to turn off the gas engines. That’s only possible with an alternative power source, like the battery packs and electric motors in the Boeing SUGAR Volt’s hybrid propulsion system. The 737-size, 3,500-nautical-mile-range plane would draw energy from both jet fuel and batteries during takeoff, but once at cruising altitude, pilots could switch to all-electric mode [see Volta Volare GT4]. At the same time Boeing engineers were rethinking propulsion, they also rethought wing design. “By making the wing thinner and the span greater, you can produce more lift with less drag,” says Marty Bradley, Boeing’s principal investigator on the project. The oversize wings would fold up so pilots could access standard boarding gates. Together, the high-lift wings, the hybrid powertrain and the efficient open-rotor engines would make the SUGAR Volt 55 percent more efficient than the average airliner. The plane would emit 60 percent less carbon dioxide and 80 percent less nitrous oxide. Additionally, the extra boost the hybrid system provides at takeoff would enable pilots to use runways as short as 4,000 feet. (For most planes, landing requires less space than takeoff.) A 737 needs a minimum of 5,000 feet for takeoff, so the SUGAR Volt could bring cross-country flights to smaller airports.—Rose Pastore
The best way to conserve jet fuel is to turn off the gas engines. That’s only possible with an alternative power source, like the battery packs and electric motors in the Boeing SUGAR Volt’s hybrid propulsion system. The 737-size, 3,500-nautical-mile-range plane would draw energy from both jet fuel and batteries during takeoff, but once at cruising altitude, pilots could switch to all-electric mode [see Volta Volare GT4]. At the same time Boeing engineers were rethinking propulsion, they also rethought wing design. “By making the wing thinner and the span greater, you can produce more lift with less drag,” says Marty Bradley, Boeing’s principal investigator on the project. The oversize wings would fold up so pilots could access standard boarding gates. Together, the high-lift wings, the hybrid powertrain and the efficient open-rotor engines would make the SUGAR Volt 55 percent more efficient than the average airliner. The plane would emit 60 percent less carbon dioxide and 80 percent less nitrous oxide. Additionally, the extra boost the hybrid system provides at takeoff would enable pilots to use runways as short as 4,000 feet. (For most planes, landing requires less space than takeoff.) A 737 needs a minimum of 5,000 feet for takeoff, so the SUGAR Volt could bring cross-country flights to smaller airports.—Rose Pastore
Sonic Boom Heads for a Thump
Sonic Boom Heads for a Thump
05.08.12

› View Larger Image
› View Larger Image

› View Larger Image

› View Larger ImageNASA's aeronautical innovators are one step closer to confidently crafting a viable commercial airliner that can fly faster than the speed of sound, yet produce a sonic boom that is quiet enough not to bother anyone on the ground below.
The key to this recent advance came when wind tunnel tests of scale model airplanes verified that new approaches to designing such aircraft would work as hoped for when aided by improved computer tools, which were used for the first time together in each step of the design process.
"That was really the breakthrough for us. Not only that the tools worked, but that our tests show we could do even better in terms of reducing noise than we thought at the start of the effort," said Peter Coen, NASA's supersonic project manager at Langley Research Center in Virginia.
Nuisance noise generated by a commercial supersonic jet's sonic booms during cruise, and by its powerful engines at takeoff and landing, has kept the speedy aircraft from entering service in the United States – except for Europe's Concorde, which was limited to trans-Atlantic flights only.
Using the computer tools, teams led by Boeing and Lockheed Martin, and funded through a NASA Research Announcement, came up with designs for two small supersonic airliners that would carry between 30 and 80 passengers and potentially enter service in the 2025 timeframe.
"In bringing their design expertise to the process, these companies are not only addressing the low boom design elements, but all of the other aspects necessary for a realistic design," Coen said.
For example, the computer tools show that one way to reduce the perceived loudness of a supersonic jet's sonic boom is to change the aircraft shape, in part, by lengthening the aircraft’s fuselage, making it much more slender. Theoretically, the noise issue could be solved by a really, really long aircraft body.
Unfortunately, while an 800-foot-long airliner may lead to publicly acceptable sonic booms, an aircraft that size still must fit at its gate, make turns while taxiing to the runway without hitting anything and generally not require an expensive redesign of the nation's airports.
"The long skinny fuselage is not a practical answer. In our pursuit of boom reductions, we examine the whole, three-dimensional shape of the vehicle including the engine configuration," Coen said. "Even then, we keep in mind that the airliner has to meet all of the other requirements which are part of good design practice."
To help reach their goals, the engineers relied on earlier studies that revealed how an aircraft’s overall configuration could modify the shape of the supersonic shockwaves coming off the airplane so that the atmosphere then reduces the sharpness of the wave. By the time the shockwave reached the ground the shock would be removed, resulting in a nearly inaudible sonic boom.
"The booms are still there, but your ear is tricked into hearing a thump," Coen said.
Two other design considerations are important. The first reduces the size of the proposed commercial airliner so it carries fewer passengers and is lighter. The second slows the cruising speed. While the Concorde cruised at twice the speed of sound, or Mach 2.0, this airliner would cruise at a slightly slower Mach 1.6 to Mach 1.8.
"These design choices not only made both the sonic boom problem easier to tackle, but make the takeoff and landing noise problem much more solvable, much more amenable to solutions with the technologies we have in hand," Coen said.
So how loud was the Concorde and how does that relate to NASA's goals of making a quieter supersonic airplane?
The measurement NASA researchers are using to base their work on is called perceived decibel level, or PLdB. Like comparing apples and oranges, PLdB is a different flavor of decibels than the measurement (dBA) often quoted when discussing how loud, for example, a rock concert is compared to a kitchen blender or library reading room.
Concorde's sonic boom noise level was 105 PLdB. The PLdB that researchers believe will be acceptable for unrestricted supersonic flight over land is 75, but NASA wants to eventually beat that and reach 70 PLdB.
"For this phase of the research, we did succeed in reducing the perceived noise level. In fact, one of the designs reached as low as 79 PLdB," Coen said. "It was a really big step, but we still have some more work to do to reach our ultimate goal of about 70 PLdB."
Additional studies already are under way to keep whittling away at the supersonic noise challenge and come up with solutions that will be acceptable to regulatory agencies such as the Federal Aviation Administration, as well as airplane manufacturers, the airlines and the general public.
And while a commercial supersonic airliner flying from New York to Los Angeles over the U.S. heartland may be another decade or two away, Coen said it's very possible that smaller supersonic business jets could debut in the skies much sooner because lighter aircraft create weaker shock waves, which makes the low boom design challenge easier to solve.
"The business jet would probably be the first on the market, and that would help introduce some of the technologies that eventually would be used on the supersonic airliner. But such product decisions belong to others outside of NASA," Coen said. "Our job is to support the science and technology behind those choices, eventually making supersonic flight available to the traveling public."
NASA Aeronautics Research Mission Directorate
Subscribe to:
Posts (Atom)